Pensamiento Lean
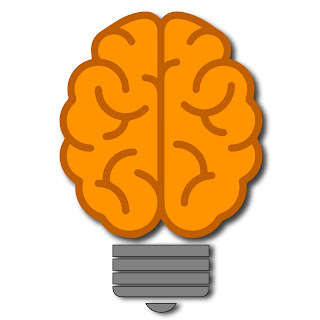
Frederick Winslow Taylor

Henry Ford
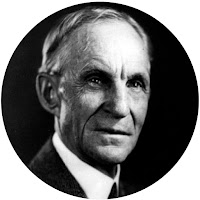
“El hombre no es quien dirige el trabajo. La cuestión es tener todas las cosas en movimiento de manera que el trabajo se dirija al hombre y el hombre al trabajo”
Ford asombro al mundo por su velocidad en la fabricación, pero sus fábricas requerían dos tipos de trabajadores claramente diferenciados. Los ingenieros quienes desarrollaban sofisticados métodos científicos para elevar la rapidez y la cantidad de producción, mientras que los operarios solo se dedicaban a ejecutarlos, este tipo de modelo de administración hacía que los conocimientos explícitos y abstractos estuvieran en manos de los ingenieros exclusivamente, y estos tenían poco o nulo contacto con el área de producción, lo que limitaba su experiencia sobre la misma.
Eijidi Toyoda
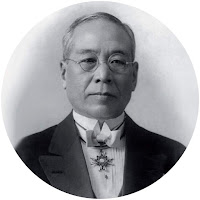
La empresa Toyota se constituyó formalmente en 1937, pero la interrupción de la producción a causa de la segunda guerra mundial y las presiones económicas posteriores a la misma hicieron que se acumularan inventarios y no se vendieran las unidades proyectadas, lo que llevo a la recién inventada japonesa de automóviles a sufrir graves problemas financieros, en 1950 Kiichiro Toyoda envió a Eiji Toyoda, su primo recién nombrado gerente general de la empresa, a Estados Unidos a estudiar los modelos de manufactura de Ford con el fin de hacer frente a la crisis.
Taiichi-Ohno

Eijidi Toyoda de regreso a Japón , luego de tres meses de haber estudiado el sistema de trabajo en la planta de Rough, en Detroit, estaba convencido, de acuerdo a lo que aprendió, que tenía que introducir los sistemas de producción en masa para solventar los problemas financieros de la empresa, Taiichi Ohno ingeniero que se incorporó a la empresa en 1943, se dio cuenta que implementar el sistema de producción en masa de Ford sería muy difícil para la realidad económica del Japón en aquel momento. La principal razón para llegar esa razón fue que este sistema de producción operaba con una gran cantidad de MUDA (despilfarro o gasto), en todas las áreas, desde el esfuerzo de las personas, el espacio y tiempos utilizados, las materias primas, el exceso de procesamientos de inventarios, etc. En su opinión, Japón o Toyoda eran demasiado pobres (en personal y recursos utilizados) para trabajar como la simple copia del sistema de producción de Ford, había que pensar en otra manera de hacerlo, y Taiichi Ohno concibió para ello tres elementos.
Grupos Kaizen
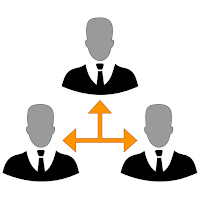
Pull System

Sí el sistema de PULL SYSTEM permitía tirar desde del siguiente proceso ¿por qué no empezar desde la orden del cliente inicial? (producir bajo demanda), este sistema fue esencial en el desarrollo del Toyota Production System.
Toyota Production System

En 1965, luego de otro viaje de Taiichi Ohno, a los Estados Unidos, se reforzó el sistema de producción de Toyota, Taiichi Ohno luego de observar los sistemas de trabajo de los supermercados norteamericanos aporto varias ideas para consolidar sistemas como el Kanban[3], el Jidoka[4] (automatización utilizando el talento de la gente) y el just in time[5] o Pull System
El Toyota Production System aporto al pensamiento lean, estableciendo un modelo de producción y gestión que combina las ventajas de la producción en pequeños lotes de producción, la producción bajo pedido, la mejora continua en los procesos y la calidad, y las economías a escala en manufactura y abastecimiento, generando con ello una gran dinámica al aprendizaje y crecimiento a lo largo de los años como sistema de producción, de gestión y como organización.
Womack y Jones describen el pensamiento lean como la búsqueda de la perfección, es decir se trata de una propuesta sistemática para la búsqueda de actividades que agreguen valor al producto mediante le eliminación de la MUDA, en todos los aspectos de los procesos de la organización.
[1] Seri (clasificación), eliminar los elementos innecesarios; Seiton (orden), ordenar los elementos requeridos en forma adecuada para agilizar el trabajo; Seiso (limpieza), limpieza diaria del área de trabajo al iniciar y al finalizar la jornada; Seiketsu (estandarización), sistema de control para lograr establecer un hábito en los trabajadores, Shitsuke (autodisciplina), comportamiento y actitud adecuada en el trabajo.
[2] Derivación de dos ideogramas japoneses (Kanjis) que significa KAI = cambio, ZEN= bueno (para mejorar).
[3] Sistema de señalamiento de la producción y el flujo de materiales.
[4] Implica la utilización del talento de las personas, es decir, su sentido común para implementar automatizaciones de bajo costo.
[5] Justo a tiempo
No hay comentarios:
Publicar un comentario